Recognizing What is Porosity in Welding: Causes and Solutions
Recognizing What is Porosity in Welding: Causes and Solutions
Blog Article
The Scientific Research Behind Porosity: A Comprehensive Guide for Welders and Fabricators
Understanding the detailed devices behind porosity in welding is crucial for welders and makers making every effort for impeccable workmanship. From the make-up of the base products to the details of the welding process itself, a wide variety of variables conspire to either exacerbate or alleviate the existence of porosity.
Recognizing Porosity in Welding
FIRST SENTENCE:
Evaluation of porosity in welding discloses essential understandings into the stability and quality of the weld joint. Porosity, identified by the visibility of cavities or voids within the weld steel, is a typical worry in welding processes. These spaces, otherwise correctly addressed, can compromise the architectural integrity and mechanical residential or commercial properties of the weld, resulting in potential failures in the completed product.
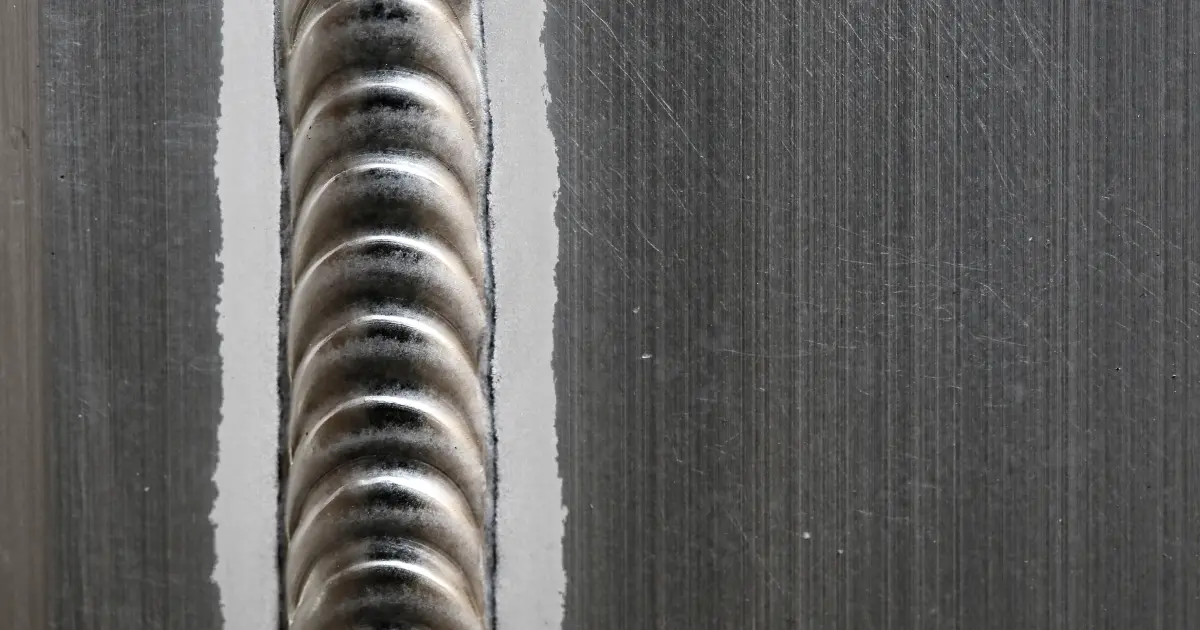
To detect and evaluate porosity, non-destructive testing approaches such as ultrasonic screening or X-ray evaluation are often utilized. These techniques allow for the recognition of interior defects without jeopardizing the stability of the weld. By assessing the size, shape, and distribution of porosity within a weld, welders can make educated choices to enhance their welding processes and attain sounder weld joints.
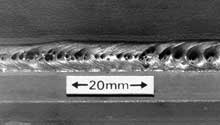
Variables Affecting Porosity Development
The occurrence of porosity in welding is influenced by a myriad of aspects, varying from gas protecting efficiency to the complexities of welding specification settings. Welding parameters, including voltage, present, travel speed, and electrode kind, also impact porosity development. The welding strategy utilized, such as gas metal arc welding (GMAW) or protected metal arc welding (SMAW), can affect porosity development due to variations in warmth circulation and gas insurance coverage - What is Porosity.
Results of Porosity on Weld High Quality
Porosity formation dramatically compromises the structural integrity and mechanical buildings of welded joints. When porosity is existing in a weld, it creates voids or tooth cavities within the product, decreasing the total toughness of the joint. These spaces work as tension concentration factors, making the weld a lot more vulnerable to fracturing and failing under load. The existence of porosity also damages the weld's resistance to corrosion, as the trapped air or gases within deep spaces can react with the surrounding atmosphere, bring about degradation with time. In addition, porosity can hinder the weld's capability to withstand stress or effect, additional threatening the total high quality and reliability of the welded structure. In vital applications such as aerospace, automobile, or structural constructions, where safety and durability are paramount, the detrimental results of porosity on weld high quality can have extreme effects, stressing the significance of lessening porosity with proper welding strategies and treatments.
Methods to Lessen Porosity
To improve the high quality of bonded joints and make sure architectural integrity, welders and producers employ particular techniques intended at decreasing the development of spaces and tooth cavities within the material during the welding procedure. One efficient approach to decrease porosity is to ensure appropriate material prep work. This consists of complete cleansing of the base metal to get rid of any kind of impurities such as oil, grease, or dampness that could add to porosity development. Furthermore, using the suitable welding criteria, such as the correct voltage, existing, and travel rate, is crucial in protecting against porosity. Maintaining a consistent arc size and angle throughout welding also aids reduce the possibility of porosity.

Additionally, choosing the right protecting gas and preserving proper gas flow rates are necessary in minimizing porosity. Making use of the proper welding method, such as back-stepping or utilizing a weaving activity, can likewise assist disperse warmth evenly and lower the chances of porosity formation. Making sure appropriate ventilation in the welding environment to remove any possible sources of contamination is crucial for accomplishing porosity-free welds. By carrying out these strategies, welders can efficiently reduce porosity and generate high-grade welded joints.

Advanced Solutions for Porosity Control
Applying advanced innovations and innovative techniques plays a crucial function in attaining premium control over porosity in welding processes. In addition, using sophisticated welding techniques click here for more such as pulsed MIG welding or changed ambience welding can likewise assist mitigate porosity issues.
Another sophisticated option includes using innovative welding tools. As an example, using tools with built-in functions like waveform control and sophisticated source of power can enhance weld quality and reduce porosity dangers. The implementation of automated welding systems with specific control over specifications can considerably minimize porosity problems.
In addition, incorporating innovative surveillance and inspection modern technologies such as real-time X-ray imaging or automated ultrasonic testing can aid in finding porosity early in the welding process, permitting for prompt restorative activities. Overall, incorporating these sophisticated remedies can significantly improve porosity control and enhance the overall quality of welded elements.
Conclusion
In final thought, understanding the science behind porosity in welding is investigate this site crucial for welders and producers to generate top quality welds - What is Porosity. Advanced options for i was reading this porosity control can further improve the welding process and ensure a solid and dependable weld.
Report this page